行业动态
在挤压筒内的铝挤压型材存在的难变形区
在挤压筒内的铝挤压型材存在的难变形区
挤压筒内的金属变形是极不均匀的,存在着两个难变形区:一个位于挤压筒和模子交界的角落处,称前端变形区,通常叫做死区,一个位于与垫片接触的后端,称后端难变形区。
在基本挤压阶段,位于死区中的铝型材,不产生塑性变形,也不参与流动。死区产生的原因是,金属沿adc面滑动所消耗的能量比沿abc面、ac面小,同时这里的金属受挤压筒和模支承的冷却,塑性低,强度高更不易于流动。
影响死区大小的因素有模角α、模孔位置、挤压比、摩擦力以及金属的强度特性和其均匀性等。增大模角α的摩擦力将促使死区增大、故平模的死区比锥模大,挤压比增加,αmax增大,死区体积减小。由图可以看出,当挤压比增加到大于13-17时,α角变化很小。实验表明,改善润滑条件,可改变α角,减小死区。在良好的润滑条件下,即使采用平模挤压,当挤压比增加到一定程度后,死区甚至会消失。热挤压因靠近模子角落处的金属易被工具冷却,使变形抗力增加,难于流动,一般比冷挤压的死区大。模孔位置对死区的影响很显然,模孔越靠近挤压筒壁死区越小。
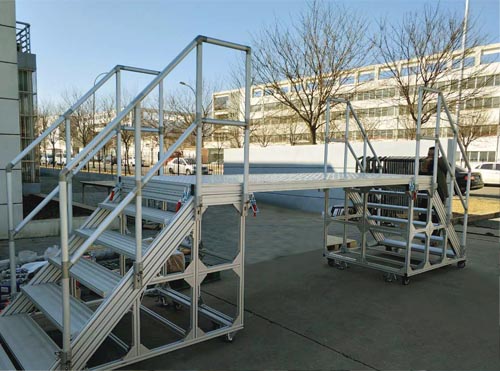
在挤压过程中,由于上述因素的变化,必将引起死区大小和形状的改变。通常随着挤压过程的进行,死区常是增大的。
死区的存在有利有弊。死区阻碍铸锭表面的缺陷及杂质流向制品表面,提高铝型材制品质量,故在实践中一般采用死区大的平模生产。但是,如果挤压过程中金属冷却而塑性降低,且挤压速度较快或挤压前金属受到强烈氧化,以及采用润滑挤压筒时,死区与塑性流动区交界处会发生断裂,在制品上产生裂纹、死皮,并加剧模子磨损。
对于后端难变形区,当挤压筒与铸锭间的摩擦力很大时,将促使金属向中心流动,但7区中的金属被垫片冷却并受到垫片上的摩擦力的阻碍作用而难以流动,从而引起7区附近的金属向中间压缩,形成细颈区6。在挤压中后端难变形区的形状和大小是不断变化的,并且在基本挤压阶段的末期难变形区7的体积变小成为7?楔形。
更多铝型材生产知识请点击:http://www.apas.com.cn